What is Blister Packaging Machine
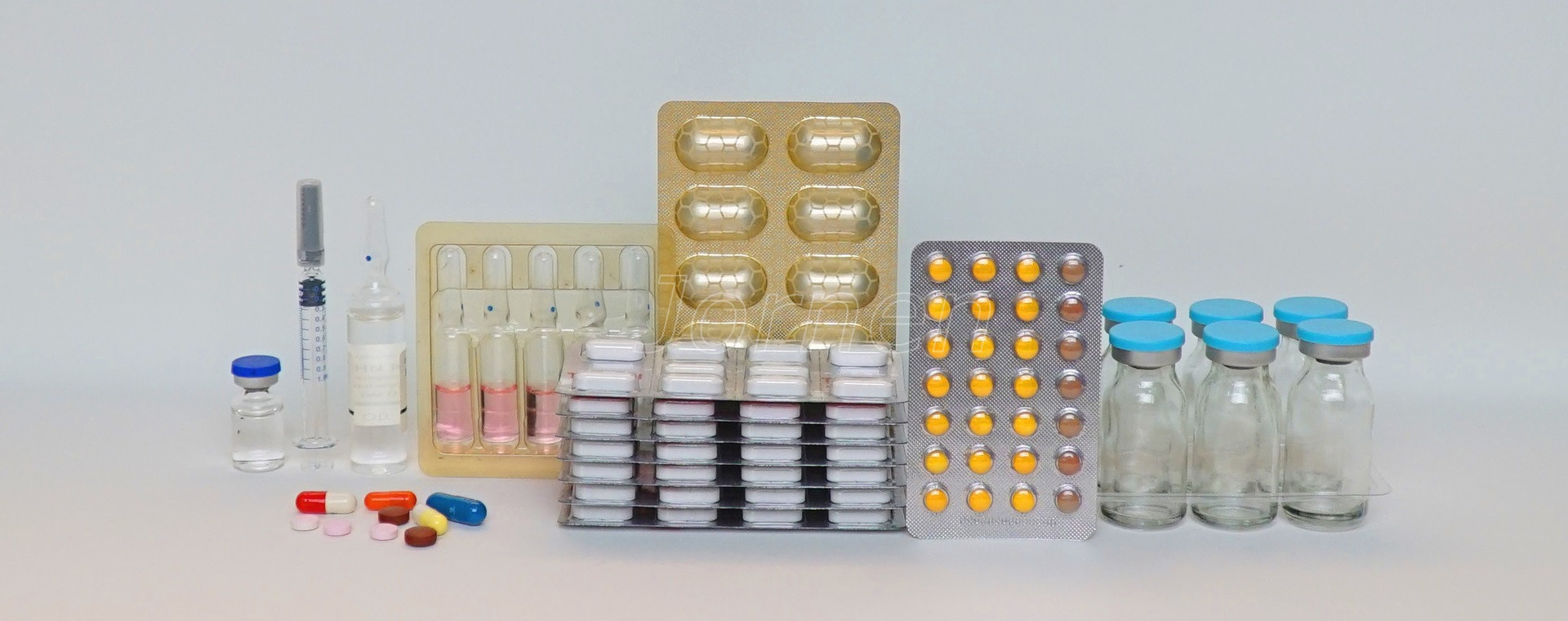
What is Blister Pack?
A blister pack is commonly used for unit-dose pharmaceuticals such as tablets, capsules, ampoules, vials, and syringes. It can also be used for small consumer goods, food, and cosmetics. Blister packs provide barrier protection for shelf-life requirements and a degree of tamper resistance.
The main component of a blister pack is a pocket made from thermoformed plastic or cold-forming aluminum film, typically backed by a lidding seal of aluminum foil or plastic.
In some parts of the world, a push-through pack (PTP) is used for pharmaceutical blister packs. It describes the two key properties of the pack: the lidding foil is brittle and breaks while pressing out the product, and a semi-rigid cavity is flexible enough to dispense the tablet or capsule by pressing it out with your thumb.
What are the advantages of blister packs?
> Blister packaging is a reliable way to maintain the quality of each drug, as every tablet is individually packaged. This means that when you remove one pill during use, it will not impact the others. In contrast, bottle packaging exposes all these tablets to the air every time you open the container. Therefore, blister packaging provides superior protection for tablets, especially those sensitive to environmental factors.
> Blister packs protect against tampering. Each tablet is securely placed in its cavity, which can only be accessed by removing the outer seal. Inspecting the packaging lets you quickly identify if someone has tampered with the medication.
> Blister packaging allows for easy tracking of medication intake. With each tablet loaded into its cavity, tracking how many doses have been taken over time is simple. For medications taken regularly, the blister pack can be marked with a date on each tablet for convenience. In contrast, bottled medicines do not offer the same level of easy tracking.
> The use of a blister pack makes identifying medication easier. For individuals who require multiple tablets at once, the blister pack can contain various drugs in a single blister card based on their dosage requirements. Following the directions on the blister card allows for easy medication management and helps prevent accidental misuse.
> Blister packs are very convenient to carry. You can take the corresponding amount of medicine when you go out. Some blister packs also have a perforation. You can easily split a well-packed pill on the Blister Card by hand (without scissors).
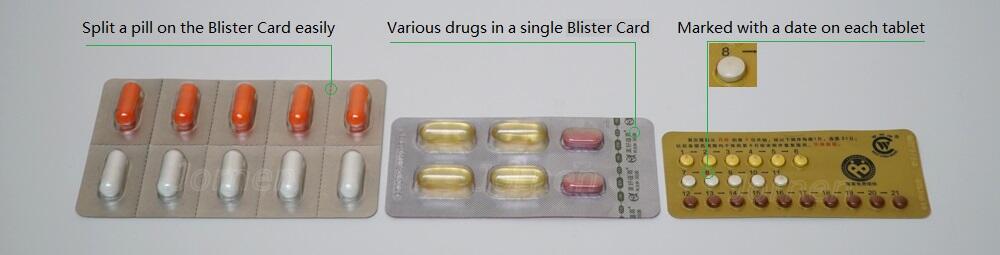
The advantages of blister packs
What is the Blister Packaging Machine?
The Blister Packaging Machine is used to create blister packs. It includes multiple stations that complete the process of forming, feeding, sealing, embossing, perforation, and punching. Two types of blister machine designs exist rotary-type and platen-type.
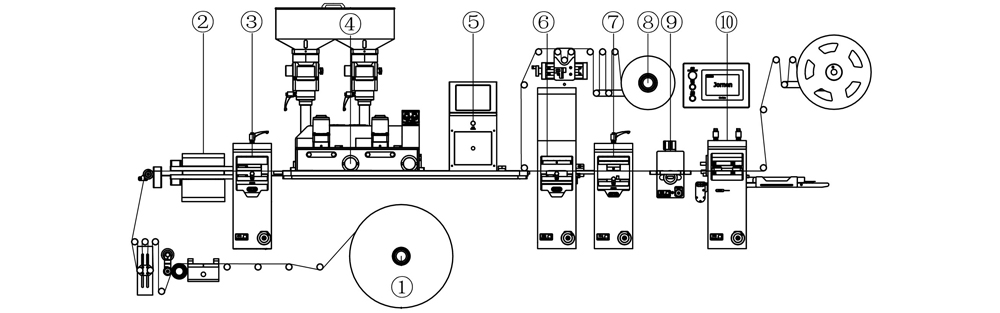
Platen-style Blister Packaging Machine
1. Forming material; 2. Heating; 3. Forming; 4. Feeding; 5. Inspection; 6. Sealing; 7. Embossing; 8. Lidding material; 9. Index;
10. Punching
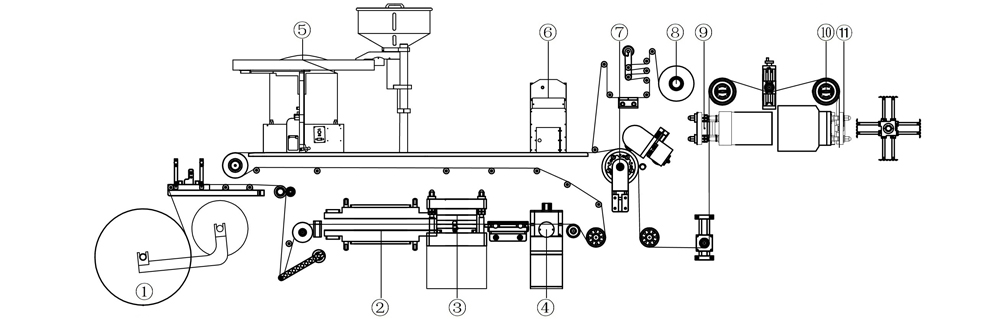
Rotary-style Blister Packaging Machine
1. Forming material; 2. Heating; 3. Forming; 4. Index; 5. Feeding; 6. Inspection; 7. Sealing; 8. Lidding material; 9. Embossing;
10. Index; 11. Punching
The forming process
Thermoforming
In thermoforming, plastic film/sheet is heated until pliable and formed into blister cavities using air pressure and molds. Complex shapes may require a “plug-assist” feature for more uniform wall distribution.
Cold Forming
In cold forming, an aluminum-based laminate film is pressed into a mold with a stamp, elongating and maintaining its shape. These blisters are known as cold-form foil blisters, which provide a complete barrier for water and oxygen, extending the product’s expiration date. However, the production speed is slower than thermoforming, the package is not transparent, and the blister card is larger due to aluminum’s inability to form near 90-degree angles.

Thermoforming Cold Forming
Blister feeding system.
Various methods of blister feeding are selected based on the product’s characteristics.
The universal feeder
The universal feeder can handle capsules, flat tablets, oval tablets, capsule tablets, triangular tablets, and other shapes. The feeder includes a hopper, a vibratory conveyor, rotary brushes, and planetary agitators that sweep the products into blister pockets. The last rotary brush has denser hairs to ensure that only correctly positioned tablets can pass out of the feeder. The feeder has a sensor to monitor tablet levels, and brushes can be easily replaced for cleaning purposes. No format parts are required for different products.
Vibratory feeder
This feeder is designed to handle capsules and various shapes of tablets, including flat, oblong, and oval. The components include a hopper, linear vibratory conveyor, disk vibratory conveyor, and grooved feeding plate. It is primarily used for continuous-motion blister packaging, where the tablets are transferred into the hopper and then onto the linear vibratory conveyor, disk vibratory conveyor, and grooved feeding plate. The pills flow down the grooves in the feeding plate and finally settle into the pockets.
Multiple Tube Feeder
The Blister Machine can be filled simultaneously with the entire index while the webbing remains stationary for the intermittent machine. The Tube Feeder can run reciprocally on the rail for the continuous motion machine, synchronized with the running webbing to fill the entire index. Blister feeding begins by transferring the capsules or tablets into the hopper, and they exit the hopper through the linear vibratory conveyor. The combo structure has an upper tray, middle tray, and lower tray that can fill the entire index of the Blister Machine at once. Capsules or tablets are loaded into the upper tray, which moves up and down with vibration, assisting capsules or tablets into the tubes. The upper tray includes a sensor for automatically monitoring the tablet or capsule level. When the story is low, the vibrator will signal to convey more capsules or tablets. The middle tray controls the pill and ensures that only one capsule or tablet is passed to the lower tray at a time. Each tube in the lower tray is aligned with a blister pocket, and when the webbing stops, the capsule or tablet is discharged into the pocket.

Universal feeder Vibratory feeder Multiple Tube Feeder
Capsule orienting & feeding device
In solid-dose blister packaging of pharmaceuticals, some customers require capsule blister packaging with an orientation function for purposes of anti-counterfeiting and for making medicine products more visually appealing.
Capsule orienting & feeding device provides the capsule orientation option. The feeding device can orientate and feed the capsules from the supply hopper, where the capsules lie randomly, into the blister cavity In a directional manner.
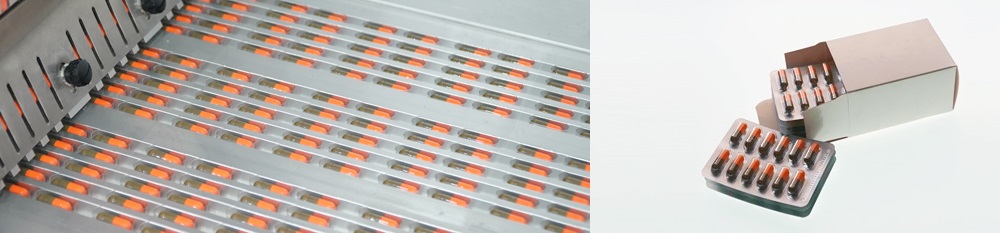
Capsule orienting & feeding device
The parenteral product feeder
The feeder moves vials or ampoules with motor-driven slides, rakes, and a servo-driven roller. The vacuum arm collects and places them gently into a formed web with a clamp-pack design that firmly clamps them in place. There are many other dedicated feeders depending on the product characteristics.

Parenteral product feeder
Blister inspection system
Quality control is crucial in the pharmaceutical industry, as improperly packaged products can lead to costly recalls and dangerous accidents. To ensure the quality of blister-packaged tablets, a camera inspection system is commonly used before sealing to detect defects such as incorrect color, size, broken tablets, empty pockets, etc. However, defects such as sealing wrinkles, unclear sealing grids or dots, crushed pills, and foreign objects can also occur after sealing. To detect these defects, some blister packaging machines now have two inspection systems, one before sealing and one after punching.
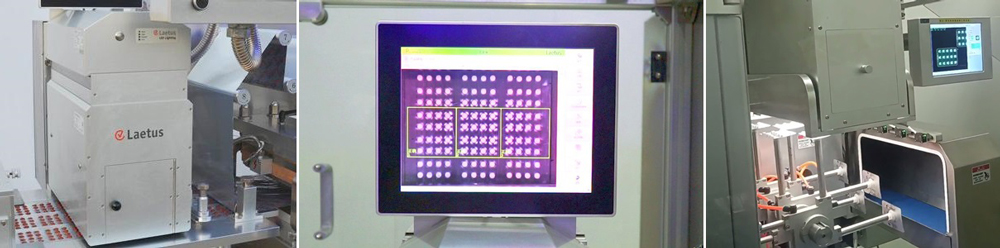
Inspection system before sealing and after punching
The sealing process
Blister sealing can be done in platen style (intermittent motion) and rotary style (continuous motion). The platen style involves the upper and lower seal mold interconnecting, repeatedly closing and separating to seal the blister web intermittently. It offers sufficient dwell time, uniform temperature and pressure across the entire sealing area, larger product blister cavities, easier manufacturing of sealing tools, a higher flexibility for selecting films, foils, and products, and more options for product feeding. On the other hand, the rotary style involves the heating roller pressing the rotary sealing mold to seal the lidding foil to the formed blister material under pressure and temperature, with continuous indexing. It allows easier blister feeding for simple-shaped products, has a shorter dwell time for sealing, requires smaller space due to a combination of indexing in one station, results in reduced wrinkles due to linear contact sealing, has a very short sealing process time, so the blister machine can run at higher speed, and can achieve higher sealing pressure with smaller forces due to a smaller sealing area (only linear).
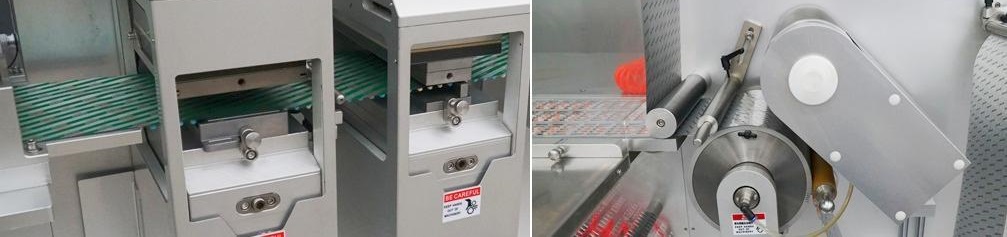
Platen sealing Rotary sealing.
The perforation process
In the perforation station, the web is perforated or notched between pockets for later separation.
The embossing process
In the embossing station, a code of letters and numbers is embossed into the sealed web, indicating the batch number and expiry date. The embossing station can imprint the code for reading from the web or the blister’s lidding side.
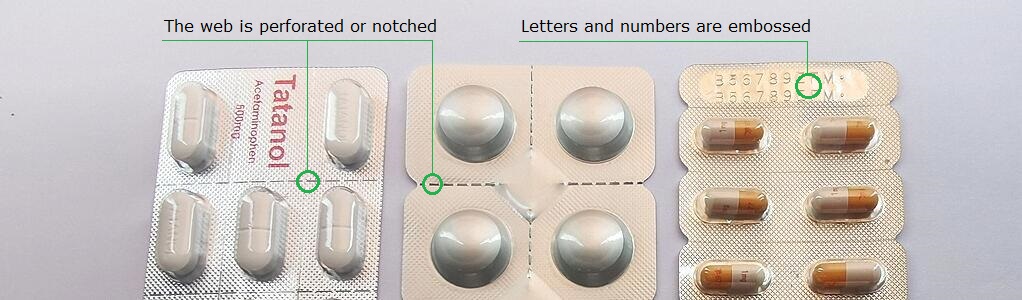
Perforation Embossing
The Punching process
In the punching station, blisters are punched out of the formed and sealed web by fixing it between the convex and concave die. Two types of punching methods are used: aligned type and crossing type. The aligned type has a smaller punching mold resulting in trimming waste of about 5mm between two blisters. On the other hand, the crossing type has cutting waste of about 1mm between two blisters, saving more material but having a punching mold nearly twice the size of the aligned type.
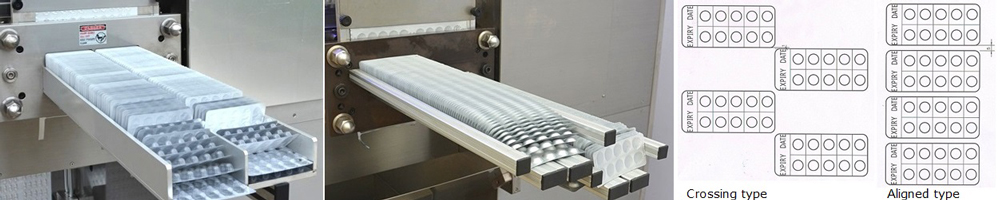
Aligned type Crossing type
What is alu-pvc-alu Blister Packaging Machine?
Blister packs come in two main types: thermoforming blister packs made of aluminum and plastic and cold-forming blister packs made of aluminum and aluminum. Thermoforming blister packs offer the advantages of easy visual inspection through transparent plastic, low-cost PVC material, and the ability to use a universal feeder. However, they have poor protective properties due to a lack of barrier against moisture and oxygen. Cold-forming blister packs offer near-complete barrier protection due to their use of aluminum but have disadvantages such as slower production speed, lack of transparency, and increased cost. To address these issues, the industry developed a third type of blister pack: the aluminum/plastic/aluminum blister pack. This type adds a tropical aluminum forming station and a second sealing station to seal the thermoforming plastic blister package with formed tropical aluminum. The result is a low-cost, easy-to-operate blister pack that offers the same protective properties as cold-forming aluminum.
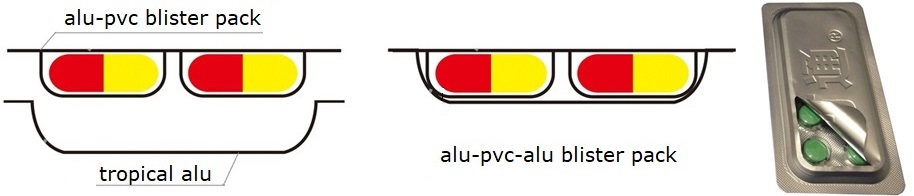
alu-pvc-alu blister pack
What is the Deblister Machine?
The Deblister Machine removes tablets and capsules from rejected blister cards produced during medicine production. It is adjustable and does not require changing parts for different blister formats. Some Deblister machines can not only automatically press out the capsules from rejected blister packs but also separate the capsules and retrieve the powder or granule, allowing the medicine to be recycled and reused. It is applicable for capsule No. 00#-5#.

Deblister and Retrieving
What is the Pinhole detector?
Alu-Alu blister packs create a barrier against water and oxygen, but the elongation-forming process may lead to pinholes, pores, and fractures that can cause the medicine to oxidize. Therefore, installing an online pinhole detector in the Blister Packaging Machine is crucial to ensure flawless blister packs and protect drug safety.
The pinhole detector uses a light emitter to transmit far infrared light across the width of the cold-formed aluminum film, and a susceptible light receiver beneath the film detects pinholes caused by unreasonable mold design, over-stretching, or defective formed film. Suppose pinholes are greater than the preset detection sensitivity. In that case, the system sends a red light signal and prompts the need to take corrective measures, such as stopping feeding the faulty blister card and rejecting it after punching.
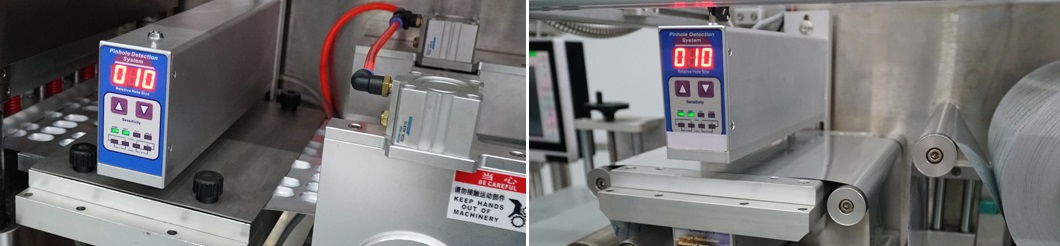
Pinhole detector for forming material and lidding material
Forming material
The most basic material for forming is PVC. PVC is low-cost and easy to thermoform but has poor moisture and oxygen barrier properties, making it unsuitable for sensitive products in humid regions. Additionally, PVC has a negative environmental connotation due to its chlorine content.
Over the years, various alternatives have been developed to improve barrier properties, including PVDC, PET, PP, and cold-forming alu.
PVDC: PVDC is coated with polyvinylidene chloride. Different coating thicknesses achieve varying barrier properties. PVDC hard sheets are commonly used in the pharmaceutical industry due to their excellent moisture resistance and ease of forming and sealing. However, PVDC films are costly and produce harmful chlorine and hydrogen chloride when heated.
PP: The advantage of using PP is its good barrier properties, ease of recycling, and non-toxicity when incinerated. Additionally, PP sheets have higher mechanical strength and lower density than PVC film of the same area and thickness, making them lighter and able to wrap more medicines. However, PP’s thermal expansion and cold contraction are more noticeable, causing significant shrinkage after heating and forming, which requires specially modified forming stations due to its specific shrinkage characteristics.
Cold-forming aluminum: The advantage of cold-forming aluminum is its effective barrier properties. However, stretching too much during forming can result in pinholes. For this reason, the blister machine should install a pinhole detector since some pinholes are too small to be detected by the naked eye. Additionally, the cavity formed is often much larger than the drug itself, which may cause difficulties in feeding.
Choosing the correct forming material for each drug is important based on their individual barrier requirements.
How to choose the suitable Blister Packaging Machine for your production?
When choosing a blister machine, finding one that fits your needs is essential. There are two types of blister machines: platen style and rotary style. Platen-style machines have a consistent speed at each station, making them slower than rotary-style machines. However, they have a more flexible mold exchange, which is better for producing medicines with various shapes like complex shapes, ampoules, vials, injections, and more. These machines are also easier to process.
On the other hand, rotary-style machines have different speeds at each station. For example, the punching station is usually several times faster than the forming station. As a result, adjusting the speed ratio when changing the mold is necessary, which can increase adjustment time (of course, the extensive use of servos has dramatically improved the adjustment flexibility). While these machines are difficult to process because their sealing mold is a roller, they are faster than platen-style machines.
If you have a lot of products, produce small batch volumes, and need to change molds often, then a platen-style machine is more suitable for you. If you don’t have a wide variety of products, need to mass-produce, and don’t need to change molds frequently, then a rotary-style machine will be a better fit.